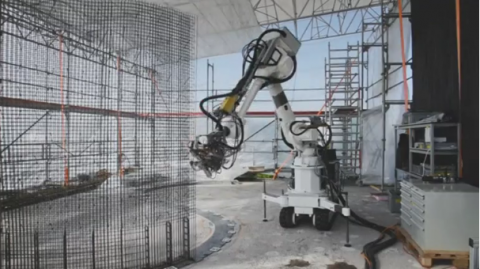
ZURICH, Switzerland (Reuters) — Construction recently began on a three-storey house near Zurich that was designed and planned using digital techniques, and is now being built using mostly robotic systems and 3D printing technologies.
The DFAB HOUSE in Dubendorf brings together a multi-disciplinary team of researchers from ETH Zurich and the Swiss National Center of Competence in Research (NCCR) Digital Fabrication who have teamed up with business partners to test new building technologies under real-life conditions.
“It’s the world’s first demonstration of how to bring together different digital fabrication technologies, both from pre-fabrication and on-site robotic fabrication,” ETH professor Matthias Kohler told Reuters.
Four construction systems are for the first time being transferred from research lab to real-world architectural applications. One is the Mesh Mould technology – a two-meter-high construction robot works in situ to construct algorithmically determined steel wire mesh designs. The “structurally optimized” mesh fabricated by the robot serves both as formwork and as reinforcement for the concrete that is poured in, according to Kohler.
“In the past we had to construct buildings with concrete by putting up formwork and then filling with concrete. That means basically you construct the building twice,” he said. “With Mesh Mould no formwork is required and robots directly build a mesh from metal which becomes the reinforcement of this concrete structure.”
The double-curved, load-bearing, wall that the Mesh Mould builds can support a ceiling the formwork of which is built using a 3D sand printer and the floors above.
The two upper floors of the house are being prefabricated at ETH Zurich’s Robotic Fabrication Laboratory using Spatial Timber Assemblies. Here, cooperating robots will assemble the timber construction elements. A similar construction process was previously used to build the Sequential Roof, a huge prefabricated timber roof structure for the main building of the Institute of Technology in Architecture; built by a robot-based assembly process out of 48,624 timber slats.
The DFAB HOUSE is one unit on the NEST platform (Next Evolution in Sustainable Building Technologies), which has three open platforms where individual construction projects can be installed.
For HiLo, another unit on NEST, Philippe Block from the Institute of Technology in Architecture at ETH Zurich, is part of a team using computer algorithms to design compression-dominant systems that are structurally strong thanks to their ‘elegant’ geometry. His team is building the HiLo unit of NEST, using ultra-light construction techniques for the floor and roof. It will feature an adaptive solar facade and is intended to produce 50 percent more energy than it uses.
“We will be building one of the units in the NEST project, and this will be the first demonstration of this system,” said Block. “I’m talking about 5×5 meter-span floor slabs, with just 2 centimeters of unreinforced concrete; that is something you can do when you get the shape right.”
The DFAB HOUSE is scheduled to be completed by summer 2018 with the three-storey building, with a floor space of 200 m2, acting as a residential and working space for researchers to test innovative smart home solutions and IOT (internet-of-things) technologies.